September 01, 2024
CPE: The Tollgates of Inventory and Financial Control
By Dr. Joel K. Faidley, CMA
~~ ~~ ~~ ~~ ~~ ~~ ~~ ~~ ~~ ~~ ~~ ~~ ~~ ~~ ~~ ~~ ~~ ~~ ~~ ~~
CPE Self Study Article & Quiz Register to gain access to the self-study quiz and earn one hour of continuing professional education credit by passing the quiz.
~~ ~~ ~~ ~~ ~~ ~~ ~~ ~~ ~~ ~~ ~~ ~~ ~~ ~~ ~~ ~~ ~~ ~~ ~~ ~~
CPE Hours: 1
Curriculum: Accounting and Auditing; Management
Level: Basic
Designed For: CPAs in business and industry; management accountants; controllers
Objectives: To explain the five tollgates of inventory movement, discuss and describe the role of the annual physical inventory, and provide examples of these concepts from a manufacturing company
Key Topics: The tollgates of inventory movement, which include receipt of material, internal failure, production reporting, Bill of Material accuracy, and shipping verification; annual physical inventory; and key concepts of the COSO Framework
Prerequisites: None
Advanced Preparation: None
~~ ~~ ~~ ~~ ~~ ~~ ~~ ~~ ~~ ~~ ~~ ~~ ~~ ~~ ~~ ~~ ~~ ~~ ~~ ~~
A major challenge for management accountants and manufacturing companies is control of operations and the resulting impact on their financial statements. The causal effects of standard operating procedures, work instructions and shop floor decisions impact financial performance of inventory centric companies.
Inventory is the lifeblood for many companies, requiring a dual focus on maintaining enough raw materials for production and minimizing cash tied up in slow-moving or obsolete stock. Corporate and plant management focus heavily on continuous improvement through lean principles and reducing process variation.
A case in point is Exide Technologies’ largest manufacturing plant and distribution center in Bristol, Tennessee. At the peak of the facility’s lead acid battery manufacturing production, volumes exceeded 30,000 units per day with 1,000 employees. The responsibility and accountability to manage inventory, production and supply chain for customer orders fell squarely on the shoulders of the plant manager, production manager, controller, and materials manager.
The site controller is viewed as the one knowledgeable in financial reporting, budgeting, forecasting, and the overall business leader for the facility since their knowledge of the causal effects of shop floor decisions had significant implications for financial results. The departments of quality assurance, engineering, facilities maintenance, distribution, human resources, and environmental health rely on the controller and the accounting department to supply insight into key performance indicators in both dollars and units of measure.
The evolution of basic policies and procedures through adaptation to new and complex reporting requirements was gradual and allowed for thoughtful improvements. The onset of the Sarbanes-Oxley Act (SOX)1 and specifically Section 404: Management Assessment of Internal Control dramatically increased the accountability of various processes at the manufacturing plant level.
Arguably, one of the most complicated and time-consuming sections of the Act is when the controller and plant manager reviewed and signed off on a large number of controls each quarter called an EICE checklist (Exide Internal Control Environment). Most of the processes the controller is accountable for are asset related and revolve around inventory and fixed assets. Accounting professionals know the importance of not over-stating assets in light of the conservatism principle and the consistency necessary when applying materiality and disclosure principles to operational decisions.
Monitoring of the five tollgates of inventory movement is critical for materials management and the desire for an annual physical inventory that results in minimal financial write-off. The tollgates include:
- Receipt of material
- Internal failure
- Production reporting
- Bill of Material (BOM) accuracy
- Shipping verification
These five check points are validated at fiscal year-end by a periodic physical inventory.
Receipt of Material
Inventory verification is not limited to cycle counts of the various raw materials, purchased parts, work-in-process (WIP) and finished goods (FG) but includes the validation of these various inventory types on the receiving docks. As an example, it is a daily routine that nearly 30 truckloads of lead (Pb) are delivered with various alloys and receiving tickets specifying the pounds and unique part numbers. One of the EICE checklist verifications calls for the dock workers to document the physical weighing of all “pigs” (60 lbs.) and “hogs” (2,000 lbs.) of each alloy type each day. (Pigs and hogs were smelter terms given to designate these blocks of Pb.)
These pigs and hogs when cast by the supplier might vary from 55 – 65 lbs. or 1900 – 2100 lbs. respectively depending on the rounding on the top of the mold and the amount of dross. The controller’s job is to ascertain these weights were being performed daily and are compared to what was entered into the Enterprise Resource Planning (ERP)2 software. Obviously, receiving 2,000 lbs. of a product onto the books when physically 1,900 lbs. is taken into possession will result in overpayment and an eventual inventory loss.
Other inventory related check points are spare parts used in the repair and maintenance of production equipment. Although not listed on the balance sheet as inventory per se, the expectation from SOX as implemented by Exide is to control materials within a facility. Exide uses a software platform to manage spare parts within a caged controlled area and maintains inventory levels to ensure parts are available to service equipment.
Exide holds about $1 million in spare parts at this facility, all of which are expensed when purchased and received. The threshold of materiality is not met, allowing immediate expense rather than capitalization of the cost until used.
SOX regulations, as interpreted by Exide’s internal and external auditors, expects monthly cycle counts to establish that spare parts inventory is being managed and controlled, indirectly proving the operating budget and forecasts are being adhered to and promoting confidence that the product’s various raw material, WIP and FG inventory accounts are being monitored daily.
Internal Failure
This rather disconcerting phrase is commonly referred to as scrap in manufacturing environments. Also called nonconforming product, scrap is a normal outflow of processes that are inherently flawed. A nominal amount of scrap is expected from destructive testing, but non-destructive scrap is a significant aspect of plant management.
Six Sigma3 is a study of process variation and seeks to align company goals with shop floor operations in continually reducing scrap and increasing the velocity of output through a pull system of inventory. Statistical process control (SPC)4 drives much of the methodology today and accounting professionals play a major role in providing data and understanding of the causal effects of production and scrap on the financial statements.
The escalating costs of quality becomes most challenging as the dollars snowball into “failure.” Internal failure is directly related to inventory on the balance sheet as external failure is the other side of “failure” resulting from warranty claims and potential liability issues outside of a facility’s four walls. Warranty claims may require product replacement, refunds or future costs like contingent liabilities for demurrage, legal fees and medical expenses. However, these potential liabilities do not affect the inventory balance carried as an asset on the balance sheet.
A primary responsibility of the site controller is to walk the plant floor daily to assess current issues and their potential impact on the weekly financial forecast. Inventory stacked up between WIP centers, extraordinary unprocessed scrap, operators standing idle, and equipment being repaired were a few of the issues to be investigated by the accounting function.
American manufacturing companies have adopted a concept called Gemba5 where management must go to “the real place” to understand the issues, opportunities and constraints facing the workers. The evolving role of accounting professionals, particularly management accountants, requires leadership both in the office and on the production and distribution floors, with a deep understanding of their businesses.
Exide was an Original Equipment Manufacturer (OEM)6 for Toyota, among others, and much of the Toyota Production System (TPS)7 was implemented to serve the customer. Japanese concepts such as jidoka, poka-yoke, 5S, and takt time8 focus on quality improvements and efficient production.
Production Reporting
Another important objective of the Gemba walks is to observe the production reporting processes that result in the creation of the next level WIP with reduction of lower-level WIP. Each successive production level adds direct materials, direct labor and overhead in the defined BOM and labor routings. Exide uses direct labor as the cost driver to allocate the overhead pool based on industrial engineering time/motion studies.
Experience associated with Exide’s past practice as a production driven company proves a tendency to over report quantities manufactured or assembled to meet the required corporate schedules9. Each pallet of production generates a bar code label with the part number and quantity, thereby relieving the sub parts used in this particular product. If a bar code is generated in error or intentionally without physical production taking place, that ghost pallet would eventually be determined as nonexistent and deleted.
The corresponding sub parts display as a negative on the costed stock status and result in a gain. The netting of the loss from the nonexistent bar code and the gain from sub parts would be an overall loss due to the conversion costs of direct labor and overhead being applied in error by the ERP system.
As detailed previously in the internal failure tollgate, the snowball effect of adding layers of cost in each successive WIP center will become a loss at some point when production quantities are overstated.
Cycle counters are employed 24/7 in both manufacturing and distribution sides of the operation to maintain control of the location of inventory produced. The unique bar codes have a unique warehouse bin location where material handlers “pick and put” these pallets in appropriate locations, which numbered over 15,000 bins. The role of the cycle counters is to continuously check the bin locations with the product located there with use of radio frequency identification (RFID)10 scanners.
Part of the SOX 404 EICE quarterly checklist is reporting and signing of bar codes that would be “killed” due to errors in production reporting. In order to maintain independence of the audit by these counters from production reporting, cycle counters reported administratively to the materials manager. In addition, these counters reported functionally to the inventory accountant and controller for resolution of reporting issues in production and also internal failure.
Bill of Material Accuracy
Tollgate four is a frequently overlooked facet of manufacturing control because if it’s in the ERP software, it must be right. Seriously though, ongoing verification of the bills of material for each manufactured product with shop floor reality is crucial for managing inventory and the potential for loss (or gains).
Competing objectives from the quality assurance function’s (QA) material usage ranges and cost accounting standards (one point, no range) adds to the potential for inventory losses. Suppose the QA standard allows for 2.4 – 2.6 lbs. of Pb to be used for a battery strap that connects the inner plates. The BOM pounds designated is 2.5 and is used for costing the product and in generating the purchase orders based on this standard usage.
QA may routinely check the mold setup and, in conjunction with shop floor operators, cast the strap at the high end of the range because of a belief that more is better in making a stronger strap. Casting to a 2.6 lb. strap would result in a 0.1 lb. loss for every battery produced in that mold setup. What if a newer mold is installed with engineered cavities to require less lead per strap with the same quality? This could result in a typical 2.4 lbs. setup and a 0.1 lb. gain per battery produced on that line.
Imagine 30,000 batteries built in one day could result in a 3,000 lb. loss or gain, which translates to more than $1,000 to the bottom line. The potential for an inventory shortage of a certain item could have severe consequences for the operation’s up time. Stocking out would result in idle labor, scrap and extra shifts at an overtime premium.
An additional facet indirectly related to BOM is the common use of substitutions for orders. If sufficient quantities of a cold cranking amp for a certain Battery Council International (BCI) Group Size11 is not available, but a larger one is, there is a cost to be incurred. Suppose the Cold Cranking Amps (CCA)12 ordered is 525 but only a 600 is in stock and the cost differential is $1.50. Fulfillment of the order, at the same sales price, will result in a substitution loss. If this substitution transaction goes unreported, an inventory loss will occur by the cycle counter or, if missed, at the annual physical inventory. Inventory errors are self-correcting. A miscount or omission in one period is typically adjusted accurately in the next count.
Shipping Verification
The final tollgate is a major threshold where fully priced inventory stock must be controlled as customers’ performance obligations are met. The transfer of ownership may occur at the facility’s docks or at delivery to the customers’ warehouses and would impact revenue recognition but that is a topic for another day.
The essence of this fifth tollgate is movement from inventory to cost of goods sold (COGS) and recording of sales revenue with accounts receivable. Exide typically has 125,000 orders open (individual batteries to be shipped) at any given time with many of those orders days out. The fulfillment of an order is very structured, with material handlers “picking” from warehouse inventory bin locations the various types and quantities for labeling and preparation on a distribution line.
Once a shipment is assembled, the pallets are “ship confirmed” in the ERP system, thereby crediting inventory and debiting COGS. The corresponding debit to the customer’s accounts receivable and credit to sale revenue would complete the transaction.
Once all pallets are loaded on a truck, the door is sealed with a tag number and the information is communicated to the security guardhouse. A final check is made by the guard, including their approval that the seal is in place. The physical custody of inventory at this stage is crucial, as an asset value snowballs through the various WIPs to finished goods. This final tollgate, as the asset leaves the balance sheet, ensures the security of full costed material movements to the customer.
The Role of the Annual Physical Inventory
To ensure the operating responsibilities are being adhered to at each of the five tollgates, an annual physical inventory is conducted to verify the accuracy of the perpetual system and the manual inputs that standard work instructions drive in the day-to-day operations. Paramount to all companies is that written policies and procedures in effect must be followed with an end-of-year physical inventory validating the processes and tollgates of control.
The importance of this annual count is shown by the presence of officials from internal audit, external auditors and supervision by the site controller. Materials planning and production personnel are excluded from the oversight due to potential conflicts of interest in the outcomes.
Assurance that proper receiving and shipping cutoffs are followed, and production/scrap reporting is completed prior to an inventory freeze on the books, may be likened to slowing the flow of a stream. It’s easiest to cross a stream when the water is down and that is similar to the time that a physical inventory is conducted.
Many companies seek to have this periodic count coincide with fiscal year end to facilitate the recording and reporting processes for inventory. Companies elect a year end at a slow time for sales to facilitate year end closings that will reduce the opportunity for errors. With expedited closing schedules, the probability of mistakes increases, impacting the financial statements.
Exide’s fiscal year end was March 31 due to that being the slowest time of year for battery demand and shipments. The annual physical was normally in late January but in recent years was moved to the third weekend of March. Stopping the flow of the inventory stream at this time of the year is easier, although still a complex event that required much advanced planning and three days to prepare, count and record the stock levels on hand.
Inventory is typically in the $20 million range and with an average turnover of 12 times, one can see the impact of the count is verification of $240 million in COGS that flowed through the facility. Even the $20 million on hand was questioned by both audit teams as to the presence of slow moving or obsolete product on hand in inventory.
To reduce the risk of intentionally not writing inventory down in the normal course of business, the Exide corporate office sought to encourage the timely write-down of inventory to saleable or recyclable values by instituting a Material Request Disposal Authorization (MRDA) process that enabled plants to write down product that was overproduced or unsold due to corporate build schedules. These scrap dollars are reclassified from the plant to the division level at the corporate office since they are responsible for the over production or reduced customer demand.
Blemished batteries are also sold for 50% off the normal cost, and this further encourages plants to do the right thing and not harbor scrap on the books at full value.
The primary problem is defining a significant inventory variance, either in dollars or as a percentage of total inventory, and determining the actions taken by corporate officials and external auditors when these limits are exceeded. This is crucial because the results of a physical inventory count reflect the effectiveness of a corporation's operational controls and confirm that financial reporting is reliable and free from material weaknesses.
Understanding corporate governance in asset valuation, particularly inventory, is crucial for financial leaders in manufacturing companies. Exide used an ERP system with real-time reporting that integrated financials with materials planning, production, costing, distribution and inventory movement.
Knowledge gained from ongoing write-downs improves estimates for contra allowance accounts and gives corporate leaders insight into policies and procedures when inventory losses exceed the annual allowance.
Key Considerations
Once an annual inventory is complete, a drill down into the data on the gains and losses by category and part number will reveal where further investigations are needed. Please see this article on the TXCPA website for questions that should be addressed.
Summary
Once an annual inventory is complete, a drill down into the data on the gains and losses by category and part number will reveal where further investigations are needed:
- Is cycle counting a robust process that adds value and not just cost to the facility?
- Are the cycle counters covering all bin locations in a systematic manner?
- Are BOMs accurate for all alloys and production WIP?
- Are there significant losses of certain types of inventory and gains in others?
- Is the receiving dock following standard work instructions?
- Is production reporting accurate? Losses in a specific WIP item type with associated gains upstream point to over reported production.
- Is budgeting for prevention and appraisal costs sufficient to mitigate internal and external failure costs?
- Does the guardhouse perform the final check consistently and raise concern when issues arise?
- Is there a culture of following policies, procedures, and work instructions daily?
- Are workers comfortable in bringing issues to supervisors or staff?
- Is a third party 1-800 fraud line needed for employees to address their concerns?
McNally13 emphasizes that COSO’s key concepts pertaining to internal control are enduring. The 2013 Framework still provides for three categories of objectives – operations, reporting and compliance – and focuses on five components of internal control – control environment, risk assessment, control activities, information and communication, and monitoring activities.
Management accountants and controllers at the manufacturing and distribution level must be the leaders for operational and financial control. But it requires more than technical expertise in accounting. Ethical leadership willing to do the right thing is a must, while developing relational skills to interact with various personalities is critical to personal and organizational success.
Understanding your industry and the COSO Framework is essential in establishing tollgates of control to ensure all stakeholders can rely on the financial statements.
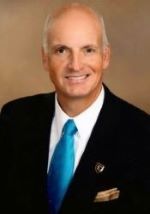
About the Author: Dr. Joel K. Faidley, CMA, is Chair and Professor of Accountancy at East Tennessee State University. Contact him at faidley@etsu.edu.
References
1. Sarbanes Oxley Section 404. https://www.sarbanes-oxley-101.com/SOX-404.htm
2. SAP. What is ERP? https://www.sap.com/products/erp/what-is-erp.html
3. American Society for Quality. What is Six Sigma? https://asq.org/quality-resources/six-sigma
4. Hessing, T. Statistical Process Control (SPC). https://sixsigmastudyguide.com/statistical-process-control-spc/
5. Lean Enterprise Institute. Gemba. https://www.lean.org/lexicon-terms/gemba/
6. Corporate Finance Institute. What is an Original Equipment Manufacturer (OEM)? https://corporatefinanceinstitute.com/resources/valuation/original-equipment-manufacturer-oem/
7. Toyota. Toyota Production System. https://global.toyota/en/company/vision-and-philosophy/production-system/
8. Quality Gurus. Glossary of Japanese Lean Terms. https://www.qualitygurus.com/glossary-of-japanese-lean-terms/#t-1675613021894
9. Einhorn, C.S. (1996, June 17). Numbers Game. Baron’s, 76(25), 36.
10. Camcode. Using RFID for Inventory Management. https://www.camcode.com/blog/using-rfid-for-inventory-management-pros-and-cons/
11. Battery Group Size. How to Choose Your Battery. https://www.autobatteries.com/how-to-choose-your-battery/car-battery-group-size
12. Walker, D. (2022). What Does A CCA Battery Ratings Mean? https://batteryspecialists.com.au/blogs/news/cca-battery-ratings#:~:text=Cold%20Cranking%20Amps%20(CCA)%20is,least%207.2%20volts%20per%20cell
13. McNally, J. S. (2013). The 2013 COSO Framework & SOX Compliance: One Approach to an Effective Transition. https://www.coso.org/_files/ugd/3059fc_c98a93b420a34d28a4c79f57db0d2c93.pdf
Thanks to the Sponsors of Today's CPA Magazine
This content was made possible by the sponsors of this issue of Today's CPA Magazine: